I leaned heavily on my expertise with industrial-level equipment and sought to gain more control over the process of FDM printing by designing and building an enclosure to maintain a stable build environment for my Prusa printer.
After playing around with a couple of designs, I ultimately choose to make an enclosure that was more functional. Using Laser-cut polycarbonate sheet, 80/20 rail and bamboo plywood, I built a sturdy enclosure while incorporating a temperature controlled exhaust fan, LED lighting and a fire suppression device for unattended operation.
Later modifications include a higher temperature hot-end and extruder along with hardened steel nozzles and upgraded x axis components. I also designed and created a dry box for in-use filament storage to mitigate hygroscopic contamination.
The resulting improvements include: faster printing, higher dimensional stability, less warping, a higher quality surface finish and the ability to use higher temperature plastics such as nylon and polycarbonate.
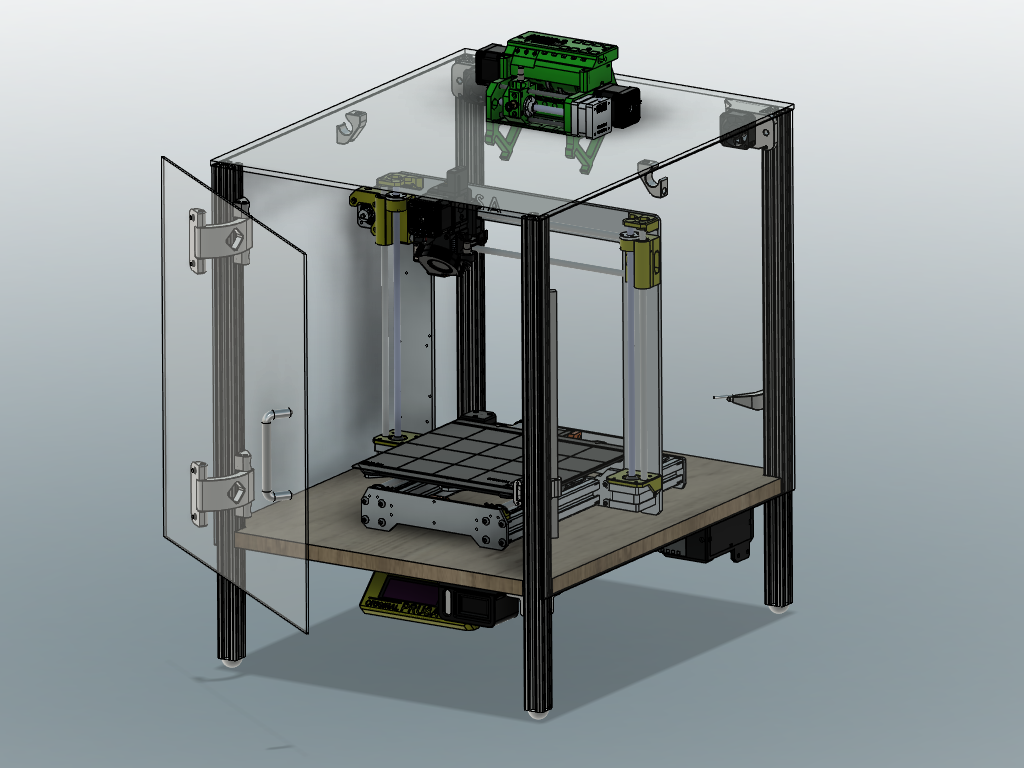
Final design with double-hinged door
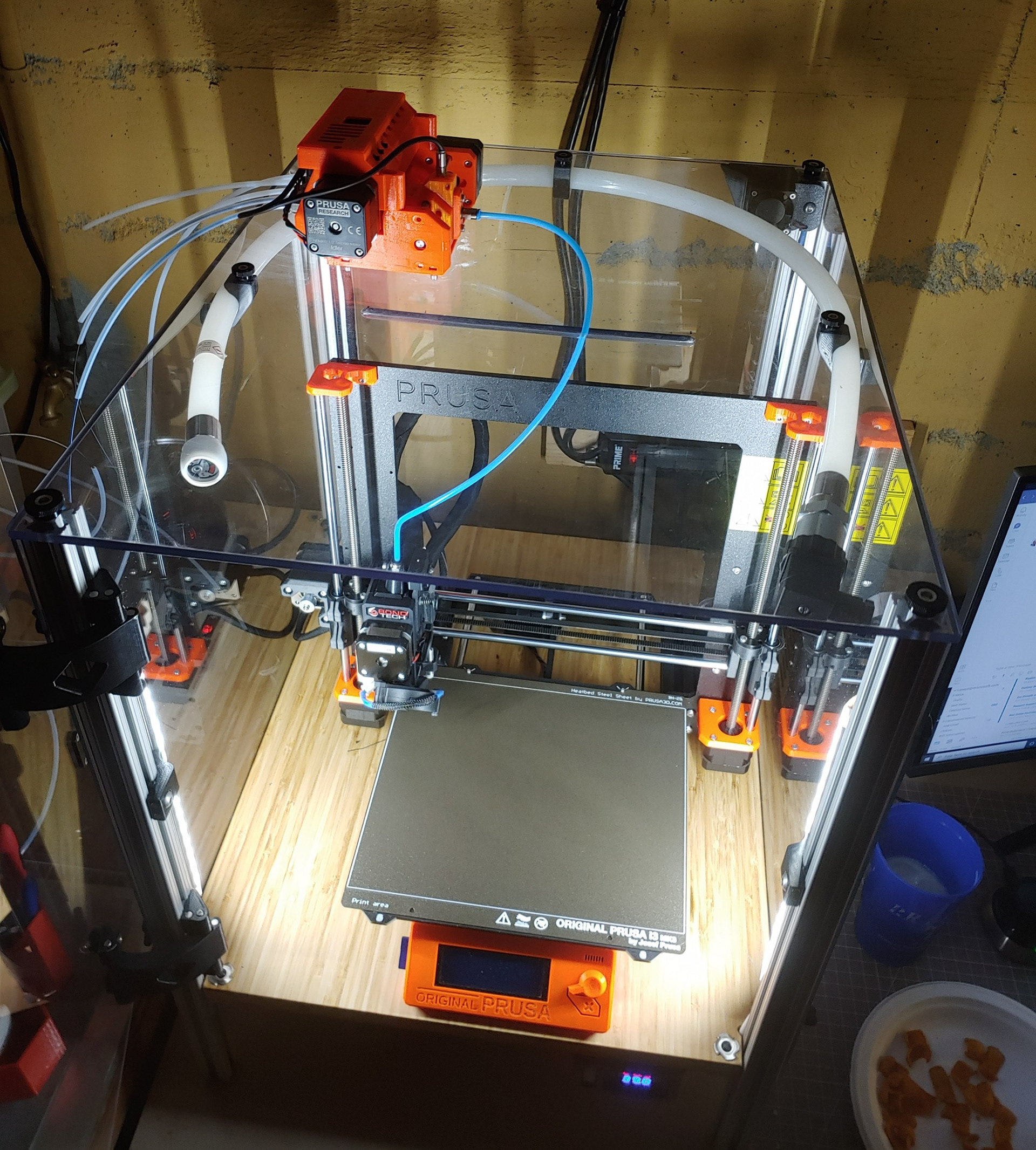
Build Chamber in use
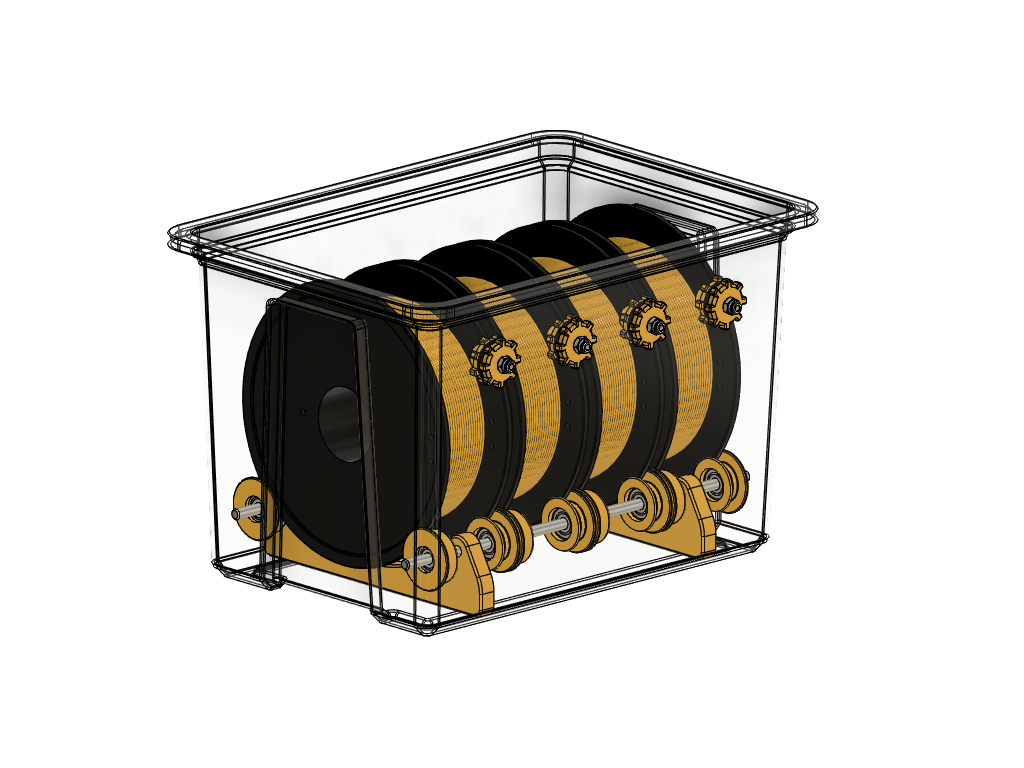
Dry box design
Build chamber in use and performing as expected